

Updating the finite element model, based on the new thicknesses and densities for the two truncated cones, was performed, and comparison between the theoretical and the experimental natural frequencies was made again. Furthermore, the two truncated cones were sent to be autoclaved for postconsolidation treatment, and changes in the thickness, density, and natural frequencies were studied afterward. Theoretical natural frequencies obtained by finite element analysis were then compared with those obtained experimentally. It was assumed that coupons that have undergone the autoclave process were fully consolidated. Material stiffness properties of these test coupons were obtained from the experiment and were used for finite element analysis. Moreover, test coupons were made using hand layup and autoclave process. The modal analysis was done on the two truncated cones in order to find the experimental natural frequencies. Also, the effect of the autoclave postconsolidation process on the thickness, density, and natural frequencies of the truncated cones was studied. In this study, the quality of two thermoplastic composite truncated cones (carbon fiber/PEEK) made by AFP was investigated from the stiffness point of view. One of the reliable tools to indicate the quality of the part from the stiffness point of view is experimental modal analysis in which one can find natural frequencies and compare them with the expected ones obtained from theory. Earlier studies show that the resulting laminate quality of in situ thermoplastic composites strongly depends on heat flux, lay-down speed, and consolidation pressure. However, due to various parameters involved in the AFP process, such as torch temperature, compaction force, lay-down speed, etc., the quality of the fiber-placed part, from stiffness and/or strength point of view, may not always be as good as desired, and in this case, the part has to undergo a secondary autoclave process. In the manufacturing of the thermoplastic composite part, it is highly desirable to reach good consolidation by using fiber placement process alone and to avoid additional autoclave process to reduce the manufacturing cost. Also, micrographs of two truncated cones were taken before and after autoclave treatment to examine the autoclave effect on the quality of the samples.Īutomated fiber placement head (courtesy of National Research Council Canada). The finite element model was also updated upon the changes in thickness and density of the truncated cones, and consequently, comparison between the theoretical and experimental natural frequencies was carried out again. After autoclave treatment, experimental modal analysis was repeated to investigate the possible changes in natural frequencies. Furthermore, the two truncated cones were treated inside the autoclave, and changes in the thickness and density were measured. Comparison between the natural frequencies obtained using the finite element method and experimental modal analysis was conducted. Furthermore, finite element analysis was performed to extract theoretical natural frequencies using material properties obtained from coupon testing. Tensile and compression test coupons were made out of the same material using hand layup and autoclave process, and stiffness properties were characterized experimentally. Then, the truncated cones were tested by impulse excitation of vibration to get experimental natural frequencies.
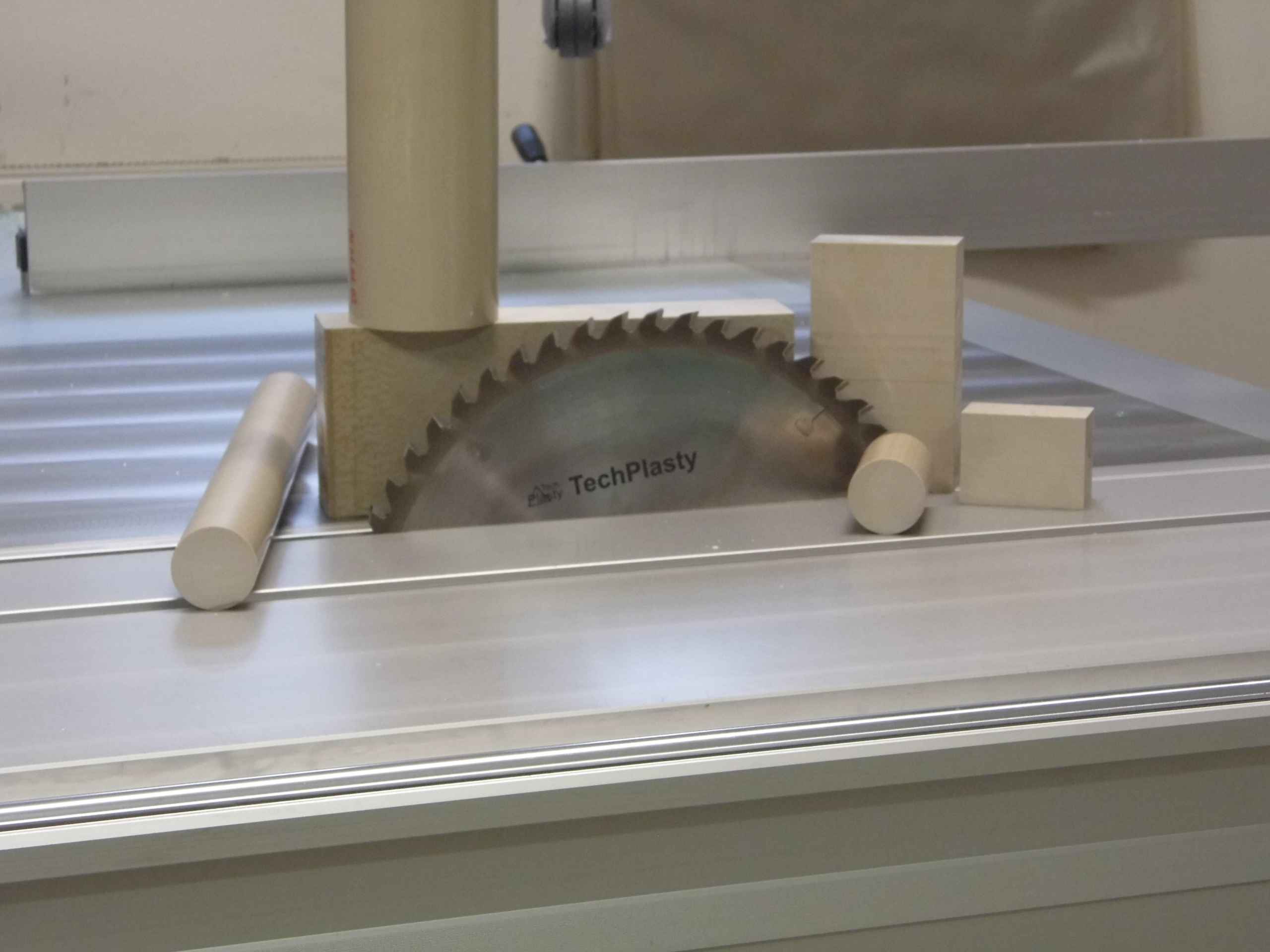
In order to investigate the effect of autoclave process on the stiffness properties of thermoplastic composite truncated cones made by automated fiber placement technique (AFP), two short truncated cones were made out of advanced thermoplastic composite material (carbon fiber/PEEK).
